Over the last decade, we have seen an increase in the use of digital twin technologies. GAM Investments’ David Goodman considers how ‘digital twins’ can fundamentally change industries by creating living digital simulation models that update and change alongside their physical counterparts.
23 August 2022
Click here to view the Disruptive Strategist newsletter in full.
Usage of digital twin technologies has now expanded well beyond manufacturing-use cases, to the world of artificial intelligence, data analytics, and IoT (Internet of Things). The adoption of digital twin technology offers a number of potential advantages, including speeding up the time to get products to market and lower maintenance operation costs, both of which are generating great excitement across multiple business sectors.
What is meant by digital twins?
Digital twin technology enables virtual replicas of physical assets to be created, facilitating a highly effective simulation. It does this by integrating data with artificial intelligence, machine learning and software, creating living digital simulation models that update and change alongside their physical counterparts.
According to Fortune Business Insights, the global digital twin market size is projected to reach USD 96.49 billion in 2029, at a compound annual growth rate (CAGR) of 40.6% 2022-2029 (source: www.fortunebusinessinsights.com/digital-twin-market-106246).
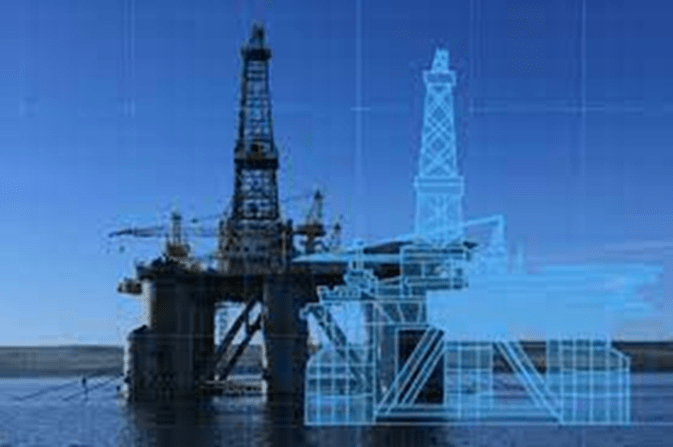
How it works
Data-driven digital twins can adapt and respond to different and fast changing environmental or operating conditions. This one-to-one mapping optimises performance by creating a real-time relationship that enables engineers to make immediate corrections to their system and rapidly accelerates new product design. It represents a new era in simulation and predictability.
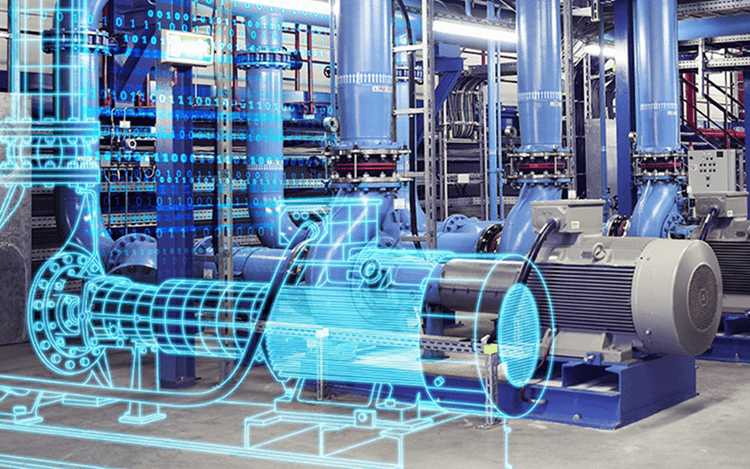
How will digital twin technology be used?
Digital twins can help in a huge number of areas, from planning, design and construction to operations and maintenance. For example, let us consider a building that has already been designed and constructed – it can have a digital twin of the entire facility, from the roof to the mechanical engineering and plumbing systems. Now imagine that the sensors in the building provide the digital twin with real-time information that updates itself according to the information provided. This enables building owners to view areas where the building is ageing or faulty and make improvements before anything fails or becomes a potential danger. These techniques are already deployed in Norway to manage bridge maintenance lifecycles.
While building digital twins is highly complicated, once set up they offer nearly limitless potential. Every individual component can be digitally replicated, from the way they interact to the environment they exist in. The digital twin then uses artificial intelligence to simulate and demonstrate the impact that changes in design, process, time or conditions would have, without ever having to subject the real-world object to those same changes.
Companies can observe the predicted use and outcomes of their products in real-time, as well as view every "what if" scenario, thanks to the shift from the actual production line to the virtual factory, which supports improved decision making and deeper understanding.
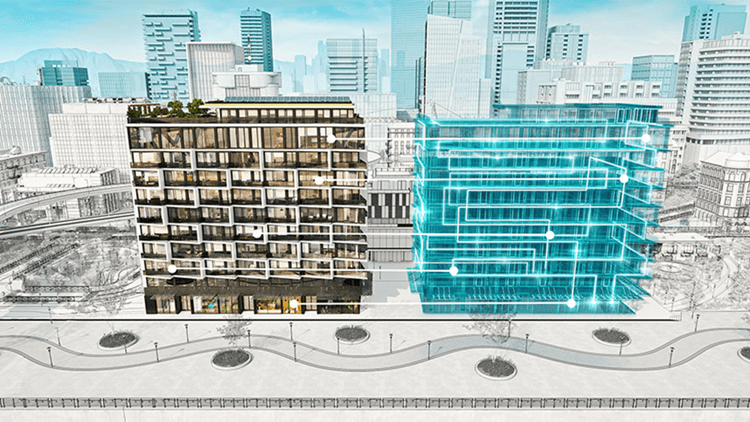
Case studies
To better comprehend how this works in practice, we will look at some real-world examples of sectors that have already made the leap.
Aviation
Using digital twins’ ability to evaluate a complete lifecycle, Boeing integrated a digital twin into its design and production, enabling it to evaluate how materials would function over the course of an aircraft's existence. The results speak for themselves, with Boeing able to increase the quality of some parts by an incredible 40%.
Automobile manufacture
A car's digital twin replicates the functions of both the software and the mechanical behaviour of the vehicle. Through modelling and analysis, many problems can be solved before a car is even made.
Unsurprisingly, Elon Musk has embraced digital twin technology at his Tesla manufacturing sites. His vehicles use digital twins to collect data that can be used to improve design, advance development of driverless vehicles, provide predictive analytics and deliver maintenance information.
Thanks to digital twins’ genuine, rather than hypothetical two-way data flow, there is almost certainly a future where vehicles will send data directly to a garage ahead of a service – describing performance statistics, parts that have been replaced, service records and prospective problems picked up by the sensors. This could have a massive time saving benefit, with mechanics able to focus immediately on the problems rather than carry out a timely inspection.
Healthcare
Many healthcare companies have already adopted digital twin technology, benefiting from huge efficiencies in patient monitoring thanks to digital twin sensors and medical device simulation.
Manufacturing
Production line machinery is business critical, expensive and comes with a lot of risk. Large amounts of data are typically necessary for huge machinery to operate efficiently; that data is being harnessed via digital twins for precise prediction of stress points and servicing requirements.
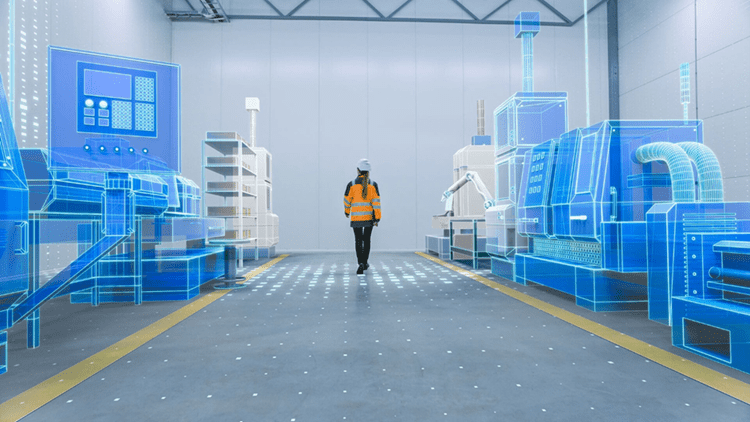
The time is right
As the benefits of digital twins become ever clearer, savvy companies have already deployed digital twins to manage the entire lifecycle of their products – exponentially increasing efficiencies over time, unlocking additional value from existing assets and dramatically lowering maintenance and operating costs. By using physics and analytics, they are eliminating unplanned downtime.
As momentum builds, it will not be long before digital twin technology is commonplace in most industries, providing data that can help avoid costly product failures and reducing some of the risks to a company’s profitability and future.
With the world experiencing an exponential improvement in computing power, storage and bandwidth, the time is right for real-time, data-driven improvements to business efficiency. Digital twin technology is just another example of these efficiencies. The pace of technological advance is unprecedented and shows no signs of slowing.
The information in this document is given for information purposes only and does not qualify as investment advice. Opinions and assessments contained in this document may change and reflect the point of view of GAM in the current economic environment. No liability shall be accepted for the accuracy and completeness of the information. Past performance is not a reliable indicator of future results or current or future trends. The mentioned financial instruments are provided for illustrative purposes only and shall not be considered as a direct offering, investment recommendation or investment advice. The securities listed were selected from the universe of securities covered by the portfolio managers to assist the reader in better understanding the themes presented and are not necessarily held by any portfolio or represent any recommendations by the portfolio managers. There is no guarantee that forecasts will be realised.